Acoustic Enclosures for HVAC Systems: Best Practices
Controlling the weather has been a long-lasting dream ever since the dawn of humanity. Take, for example, the anthropomorphic gods and mystical entities that have influenced the climate in various stories and myths. Humanity achieved this dream when we created the HVAC unit.
This inseparable addition to modern-day living has its price. And we are not talking about the obvious financial one. HVACs often come with noise. Disruptive airborne and structural sound interference that ruins relaxation, focus, and recovery. Now the dream is to control the noise from the air conditioning system.
Thanks to acoustic enclosures, this dream would be just a quick nap. These solutions are precision-engineered shells that contain, absorb, and isolate sound before it spreads, addressing the issue at its very source.
Understanding Acoustic Enclosures
Powerful mechanical equipment, like chillers, air handling units, or rooftop HVAC assemblies, usually produces airborne and structural sound. They are not pleasant to be around, but they are typically placed in highly populated areas.
We have had multiple projects where an office building and a residential complex are trying to coexist, and an HVAC unit is exposing both to constant noise levels.
Acoustic enclosures are different from louvres or duct silencers, which treat sound travelling through airflows. Enclosures address the direct propagation of noise, coming from the machine itself.
They are made of galvanised or powder-coated steel, made into a rigid structural frame, and filled with sound-absorbing materials. The combination of mass and absorption allows the enclosures to both block and dampen sound energy across a broad frequency spectrum.
Key functions of an HVAC acoustic enclosure include:
- Preventing airborne sound radiation from vibrating machine surfaces.
- Limiting vibration transmission to building structures.
- Preserving operational access through removable panels, inspection windows, or hinged acoustic doors.
- Facilitating ventilation using attenuated airflow paths and silencers to avoid heat build-up.
The result is a self-contained acoustic control unit. With it, the machine is both acoustically and mechanically isolated from the rest of the environment. This is especially valuable in densely populated urban zones, data centres, or facilities with strict environmental noise regulations.
Why HVAC Noise Needs Special Treatment
One can get the wrong impression by only looking at their rectangular shape, but HVAC systems have a complex noise profile. They generate a blend of tonal and broadband noise. Here lies the complexity.
A single-point noise source is much easier to treat, but that rarely, if ever, is the case with air conditioning units. Tonal noise stems from motors, fans, and belts that operate at fixed speeds. This produces the famous hum of the unit. While airflow turbulence, or compressor cycling, generates a wider range of frequencies, making it harder to isolate and control.
Steady noise, or hum, is predictable and therefore easier to isolate and control. The trouble is that HVACs often combine that type of noise with Intermittent noise. Compressors and condenser fans can create unpredictable bursts of noise as they cycle on and off. This inconsistency pushes people to perceive the sound annoyance more noticeably.
Typical HVAC noise sources include:
- Axial and centrifugal fans
- Compressors and condensers
- Electric motors and pumps
- Vibration transmission through frames, mounts, and duct connections
Research, like the one published by Dr Mathias Basner, MD, links chronic HVAC noise exposure to reduced cognitive performance, increased stress, and sleep disturbance.
This is particularly noticeable when units are located near office zones, hospitals, or residential blocks. Urban areas with reflective surfaces only intensify the problem by causing the sound to bounce unpredictably between buildings.
HVACs require precision-engineered acoustic enclosures that account for airflow, vibration, and tonal content simultaneously.
Design Best Practices for HVAC Enclosures
Effective acoustic enclosures have to take into account airflow, safety, and maintenance access. A successful design begins with understanding the acoustic profile of the unit and tailoring the solution to its specific demands.
That is why you can’t just buy a ready-made solution and install it like a lightbulb. You need acoustic experts to inspect the situation and provide guidance on the best approach to HVAC soundproofing.
Expert-led Approach
- Start with a site-specific acoustic assessment
Measure how loud the HVAC system currently is (in decibels), and figure out how much quieter it needs to be to avoid disturbing nearby spaces like homes, offices, or hospitals.
This helps you set a realistic sound reduction goal and make sure your design will meet local noise regulations (like EU Directive 2002/49/EC or ISO 11690 for workplace noise). - Design for thermal management
HVAC systems generate a lot of heat, so your enclosure must let air in and out. Use silencers or acoustic louvres to maintain ventilation while keeping noise inside. If natural airflow isn’t enough to keep the equipment cool, add fans or mechanical systems to actively move air; this is called forced ventilation. - Use high-performance acoustic materials
Enclosures typically combine steel cladding, mineral wool or foam infill, and mass-loaded layers to block airborne sound and absorb reverberation. Choose non-combustible and moisture-resistant materials to extend service life. - Minimise vibration transmission
Use anti-vibration mounts, floating floors, or isolation pads to decouple the enclosure from the floor or surrounding structure. This stops structure-borne noise from leaking out. - Prioritise modularity and service access
You don’t want inspectors to write you up or give you a fine because they didn’t have access to the unit. Equip enclosures with removable panels, maintenance hatches, and sight windows to allow routine inspections without disassembly. For rooftop or compact installations, modularity ensures quick assembly and easier transport. - Avoid acoustic shortcuts
Even small openings can let sound escape. Make sure every joint, cable entry, and duct connection is sealed properly. Use materials like rubber gaskets, special sealants (acoustic caulk), or overlapping panels to block noise from slipping through. - Model performance before fabrication
When going to an expert such as DECIBEL, ask for Finite Element Analysis (FEA) or Computational Fluid Dynamics (CFD). With these techniques, we can simulate noise propagation and ventilation efficiency all on a conceptual level. This reduces risk and saves cost at installation because it gives you a detailed simulation on a screen that allows you to see how different solutions would affect your HVAC system.
Material and Construction Considerations
There are 3 fundamental aspects of an effective acoustic enclosure: How heavy is the frame (mass), how well does it stop vibration (damping), and how much sound energy can it take in (absorption). Each principle has to be carefully calculated and combined with the rest for the solution to work properly.
1. Mass – Stopping Airborne Sound
Mass is the first and most straightforward barrier to sound. According to the Mass Law, the denser and thicker the material is, the more it resists sound wave transmission. This is especially true for low-frequency noise, which is common in HVAC systems.
- Materials like steel, concrete, or high-density fibreboard are used as the outer skin of the enclosure.
- A heavier enclosure wall can block more sound, but adding mass also means structural support must be considered in the design.
2. Damping – Controlling Vibration Transmission
Sound can travel through the enclosure itself, especially when components vibrate. That’s where damping comes in. Damping materials convert mechanical vibration into low-grade heat, breaking the chain of transmission.
- This usually involves adding a viscoelastic layer between two rigid panels.
- It’s especially important near mounting points, fasteners, or any location where equipment is directly attached to the enclosure.
- Without proper damping, an enclosure might amplify noise like a drumhead, even if it’s made of heavy steel. Which defeats its purpose.
3. Absorption – Soaking Up Internal Reflections
Once sound gets into an enclosure, it can bounce around inside and build up pressure. Absorptive materials are used on the internal walls to soak up this energy before it escapes.
- Common materials include acoustic foam and mineral wool.
- These are typically installed behind a perforated metal lining so that sound can reach the absorbing layer.
- Absorption helps with mid- and high-frequency noise, such as motor hum.
The Components of a Typical Enclosure
- Outer steel sheet (for sound blocking and weather protection)
- Mid-layer damping compound (to reduce vibration)
- Inner acoustic infill (for absorbing sound)
- Perforated inner lining (to protect the infill and let sound waves reach it)
Fire Safety and Durability
Outdoor HVAC units live with the elements. So the materials for the enclosures must be fire-resistant, corrosion-proof, and weather-sealed. Galvanised or stainless steel is commonly used, with protective coatings to withstand rain, wind, and UV exposure.
Integration with Other Noise Control Elements
Even though this article focuses on solving HVAC noise, the reality is that these systems are rarely standalone. Any solution would work much better if there were an all-encompassing soundproofing strategy that considers the full mechanical system or architectural approach.
Enclosures suppress sound to a great extent, but partnered with vibration control, duct attenuation, and building insulation, they can be far more effective.
- Vibration isolators: Use spring mounts, anti-vibration pads, or rubber feet under HVAC units to prevent mechanical noise from travelling through structural supports and into floors or walls.
- Duct silencers or acoustic baffles: Enclosures may contain airborne sound at the machine, but noise can still escape through connected ductwork. Installing silencers helps absorb sound before it reaches occupied spaces.
- Building envelope treatments: In environments where low background noise is essential, noise control must go beyond the machine room. Applying acoustic treatments to walls, ceilings, or service shafts ensures that sound energy is contained.
Acoustic enclosures are just a note in the symphony of building soundproofing. There are so many solutions available on the market that ignoring the noise from your HVAC system is just not a good idea, from both regulatory and user perspectives.
These enclosures isolate the noise from the machines, but they should not be isolated themselves from a coordinated acoustic design blueprint.
Get in touch to learn how DECIBEL can help you design and implement high-performance acoustic enclosures!
LATEST BLOGS
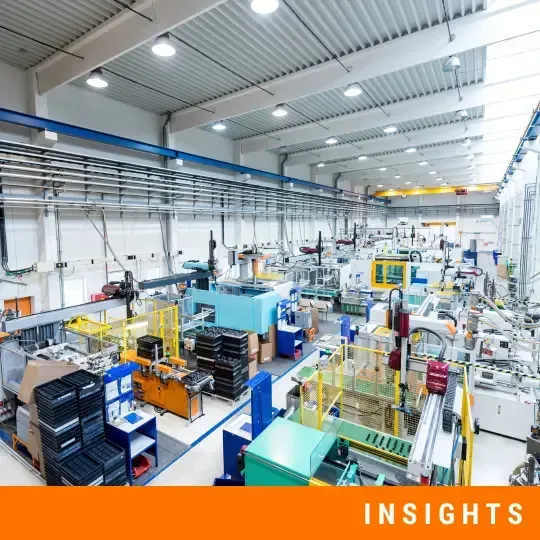
19.08.2025 Five Signs Your Facility Needs Professional Acoustic Treatment

15.08.2025 How Noise Control Improves Accuracy in Laboratory Testing

13.08.2025 The Critical Role of Acoustics in Modern Educational Facilities
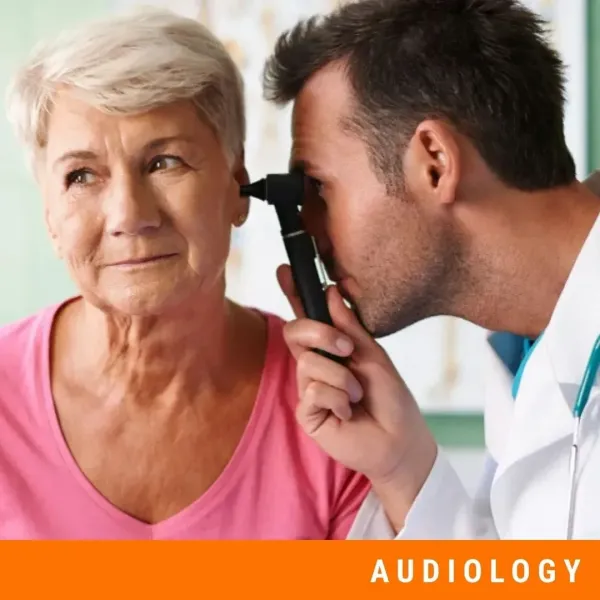